|
I met Russell McCumber in 2001. He was in 5th grade and well ahead of his classmates. Rather than push him still further ahead, his teacher and his parents decided that during 6th grade he should take one day a week off school, and do some sort of apprenticeship. That's how it was that during the 2001-2002 school year Russell spent one day a week with me and constructed a violin. |
First off, let me point out that when an adult enters violin making school he or she spends five days a week, from 8:00 till 3:00, working on instruments. Despite this large amount of time, a student usually takes about a year to complete his or her first violin. Now, with Russell we had one day each week, not as many hours for that one day, and he was 11 years old. Clearly I had to rethink the usual curriculum.
|
|
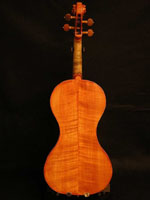 |
The main thing we did was to simplify the instrument. The violin he made is guitar-shaped so as to avoid having to shape corners. It has both a flat top and a flat back, which saves a huge amount of time over carving an arch and meticulously thicknessing each part of the arch to a different thickness. He designed his own sound holes and head, and cut the pegbox clean through rather than leaving a floor. He installed purfling on the top only, as it is not needed, structurally, on the back. |
I hear some people crying out aghast and befuddled. Do not fear, it sounds great and we maintained all the important aspects to make it playable.
It may come as a surprise to some, but Stradivari himself made some guitar-shaped violins. I have heard that this was to settle an argument over whether or not the corners on a traditional violin have any acoustic importance. Strad maintained that they do not, and he made instruments to prove it. Joshua Bell plays on one of them. We took a 1715 Stradivari violin and modified its shape to eliminate the corners. |
|
|
The flat top and back were more of a guess on my part. Fortunately they turned out to work quite nicely. Since the traditional arch helps the top resist the downward force of the strings, we left both top and back thicker than usual. Many might think that this would mute the tone, but a flat piece of wood is much more flexible than an arched one, so the vibrations travel more easily. Think of the tone of a flat-top guitar versus an arch-top. The flat-top generally has a warmer, darker sound, speaks and responds more easily, and has better sustain. The arch-top usually has a more glassy, sparkley, tone and more differentiation of the notes for fast passages. |
We installed a traditional bass bar and soundpost to reinforce the top and help transmit acoustic vibrations along the top.
The sound holes need to cut the top across the proper area, to free the top up to vibrate easily. They also need to have sufficient surface area to allow easy air movement. Other than that they can be any shape at all. Dr. Thomastik, a physicist and founder of the Thomastik string company (maker of Dominant strings), made a fascinating violin with what he called shell-shaped sound holes. Russell designed his own. |
|
|
Pegbox and head can be modified greatly. The head can be any shape at all as long as it's about the right weight. The pegbox needs to be shaped such that it can hold the pegs properly, but beyond that there are no limitations. Traditionally a floor is left in the pegbox, but this makes it much harder to carve and sometimes even makes it harder to thread strings into the pegs. Russell designed his own head and cut the pegbox clean through.
|
Purfling is an inlay that is morticed into the top and back near the edge. (Those two black lines around the edge of most violins.) It's primary purpose is to prevent cracks which form at the edge of the top from propagating into the center of the belly. The back, being maple rather than spruce, is not so susceptible to cracks, and therefore doesn't really need purfling. Russell installed purfling inlay on the top.
|
|
Russell made the fingerboard on this violin of eastern hophornbeam so as to avoid using ebony, a rainforest wood.
Details, details. The pitch of the neck and height of the bridge are a bit higher than usual. This is to provide adequate bow clearance at the edges of the top, since there is no arch to the top. Russell varnished this violin with a shellac based spirit varnish, known to the trade as 1704. The back and neck are made of bigleaf maple cut in the northwest US. The top is spruce also from the northwest US. The pegs, tailpiece, and chinrest are commercial products made of boxwood. Very few makers make their own fittings.
It took more than the school year, about a calendar year, for Russell to complete his violin. He was 12 when he finished. Russell now plays on the instrument he made. From all accounts (namely from his parents and his music teachers) it has had a dramatic effect on his violin playing and practicing. Apparently this is the secret for how to get your children to practice without any fighting....
All in all this project was quite an experience for myself as well as for Russell. Many people have asked me about doing a similar apprenticeship with their son or daughter. I have toyed with various ways to go about it -- especially with a few children at a time -- but for the moment I don't have any immediate plans. If you have ideas about this please contact me; I'd be happy to consider them.